The following is a comparison of the tried and true Prusa 3D printers and those from their upstart rival, Bambu Lab. While I think it is a useful comparison for anyone trying to decide between the two brands, it is geared specifically to shoemakers looking to 3D print shoe lasts, orthotics, heels, and even entire shoes. Note that when I say shoemakers, I’m referring to those making shoes on a small scale, like orthopedic, fashion, and hobbeist shoemakers. Big companies can obviously use 3D printers that cost drastically more!
I should add that I have only personally used the Prusa MK3S (No MMU) and the Bambu Lab X1C (with AMS) models, so I will be mainly talking about them. But I will also keep the Prusa XL and other models from these brands in the discussion. The main reason I’m comparing only these two brands is that I have previously recommended Prusa to shoemakers and wanted to give an update now that I’ve spent some time with a Bambu printer. And while there are numerous other good brands out there, I think these two are in a class of their own.
Quality and Reliability
If there is one thing that can’t be compromised on, it is the ability to reliably produce quality parts. It doesn’t matter how many bells and whistles a printer has, if it commonly runs into issues mid print, then it is no good. Both Prusa and Bambu Lab do great in this category. When comparing my Prusa MK3S to my Bambu Lab X1C, I would say that the latter does a bit better. I particularly like the excellent first layer. But Prusa’s new MK4 also has similar tech allowing for perfect first layers among many other advancements. For the purposes of shoemakers, I would say that both Prusa and Bambu Lab printers provide excellent quality and reliability and any differences between these two isn’t enough to justify choosing one over the other. One caveat though is that I have only used my X1C for a few months while I have had my MK3S for years.
Speed
Bambu Lab leverages CoreXY architecture which is considerably faster than i3. Rather then swinging the part back and forth (bed slinger), it is the toolhead that moves (in a very clever belt configuration).
Bambu Lab was also out the gates first with input shaping, a software compensation for hitting resonance frequency. Prusa has answered with their own input shaping. But with large parts, I don’t think a bed slinger will gain as much from it as CoreXY. All this being said, the bottleneck for shoemaking applications seems to be more ability to melt plastic fast rather than how fast the tool head can be moved. But nevertheless, I still find the X1C to be about twice as fast as the MK3S for shoemaking applications. High flow nozzles may help leverage the full speed potential of CoreXY and input shaping. Neither company has tackled this yet, but there are third party solutions available.
Remote Control and Monitoring
One area where Bambu Lab and Prusa printers diverge is in how they are controlled and monitored. While Prusas are very reliable to use with SD card storage and simple printer controls, I find the lack of remote control and monitoring is clearly a deficiency after using Bambu Lab’s printers. With the X1C, I can send the print directly from the slicer and monitor it there via the built in camera along with temperature and humidity sensors. The app also allows for remote control and monitoring, which is fantastic. Prusa is making progress with remote control and monitoring, but they have never given nearly enough emphasis in this area in my opinion.
Multi-material
Firstly I’ll say that I have never used Prusa’s multi material unit. I just heard too many reports of it being a pain to use. And just looking at it all I see is a jumbled mess cables and so on. Bambu’s automated material system (AMS), on the other hand, is a sleek package that also happens to store filament and keep it dry. And now that I’ve had a chance to use it, I can agree with so many others out there and say that it is an excellent addition to the printer. One downside of both the MMU and the AMS is how much material is waisted on filament changes due to the need to purge from a single nozzle. The Prusa XL addresses this issue by employing a tool changer with multiple heads, but at the expensive of complexity and cost. So if you can find ways to minimize filament changes, like only using a different interface material, then the AMS can work out quite nicely. Furthermore, this is a moot point for my favorite use of the AMS, and that is handling material run-out for large prints like shoe lasts by loading the same material from the next available reel.
Build Volume
Despite a similar footprint, the Bambu Lab printers have a larger build volume (256mm x 256mm x 256mm) than the Prusa i3 printers (250mm x 210mm x 210mm). This small difference might not sound like much, but it happens to be just the right amount for shoemakers. By going diagonally, even size 14 shoes can be 3D printed.
Enclosure
Enclosures are important for preventing warping of large parts and high temp materials. They also keep dust and debris away from the printer, keep hands away, potentially reduce risk of fires, look nice, and perhaps most importantly, help deal with fumes. Prusa’s aversion to enclosures has always boggled my mind. Sure they now have one for the i3 printers, but it is a clumsy afterthought. And despite how well suited CoreXY printers are to enclosures, the Prusa XL by default comes without one. Bambu Lab, on the other hand, has gone all in and created a fantastic enclosure, even including a carbon filter and software that makes it easy to use the printer as a filament drier. A quick note I would like to add though is that the X1C enclosure does not entirely deal with fumes on it’s own; some still enter the room. That’s why I’m planning on venting mine.
Support, Community, and Repairs
One of the reasons I went with Prusa in the first place so many years ago was that I’d heard they had both great support and a great community. I was new to 3D printing and didn’t want to be left hanging when I encountered issues. I definitely made the right choice. So I had my reservations that Bambu Lab would not be as good in this category. But while their support hasn’t been quite as speedy, I have still gotten all my questions answered. And it’s quite surprising how a massive community seems to have been created overnight, despite Bambu just having completed their Kickstarter not so long ago.
Something else I like about Prusa was how repairable and upgradable their printers are. Bambu has taken note of how much the community appreciates this and so their spare parts are cheap and accessible. And third parties are now starting to make parts too. Whether or not Bambu’s printers will be as upgradeable is yet to be seen.
Interestingly, Bambu has recently also launched MakerWorld which is their version of Prusa’s Printables, a community driven repository for 3D models. It seems they are trying to match Prusa step for step. The question many people are wondering is: What will happen if they overtake Prusa? Will they still be so ambitious?
Price
Bambu Lab recently launched the P1S which only has minor differences from the X1C. It is $699 US or $949 with the AMS. The Prusa MK4 is $799 but that is a kit you have to assemble and the enclosure and MMU are extra. So pricing of their primary models isn’t all that different. Then there is the XL which with five tool heads and fully assembled will cost $3999 plus considerable shipping unless you are in the EU. Unless you are doing quite a bit of business, this is hard to justify. Hobbyist for sure will be far better served with one of the primary models.
Bambu Lab definitely has price advantage by manufacturing in China. And they have benefited enormously from open source work, particularly that by Prusa. At the same time Bambu Lab isn’t nearly as open source themselves. This is a very controversial topic and much of the 3D printing community is polarized by it. So perhaps it’s something to think about when considering one of these two brands.
Prusa XL
I’ve been one of the many many people waiting for a Prusa XL for over a year now. As one can guess from the name, it has a huge build volume, 360mm cubed to be exact. This is sufficient for even the largest feet. it employs tool changer technology which has some big advantages over using a single nozzle in multi material systems. Specifically, using filament with different properties works seamlessly, whereas trying to manage this through a single nozzle creates a lot of headaches. For instance, you don’t have to waist time and material purging filament (this can be a lot!). Furthermore, flexible materials can be used in multi-material prints with a tool changer, whereas in the AMS or MMU, they are likely to result in a jam (though there are exceptions). So if you are interested in 3D printing multicolor soles or entire shoes, a tool changer is the better way to go.
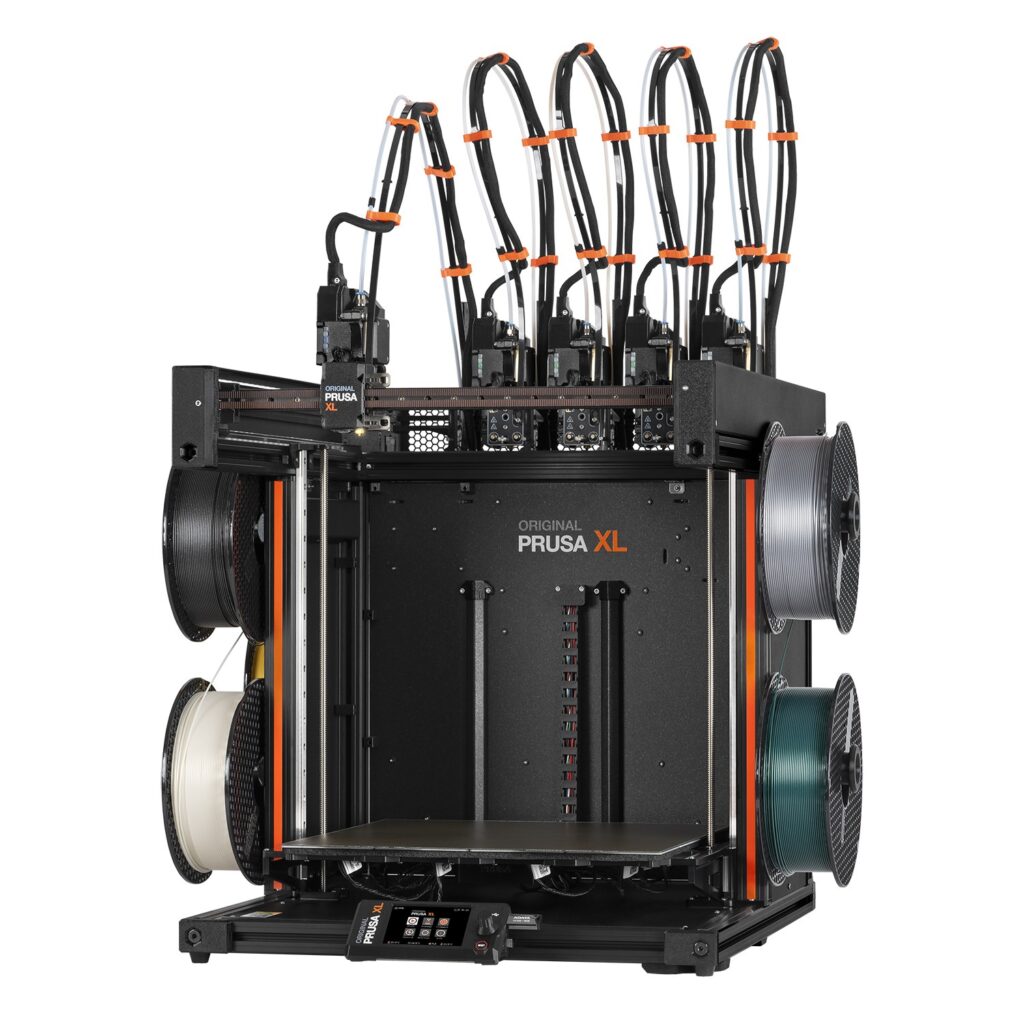
But the Prusa XL is still in short supply (I think they might still be filling day 1 pre-orders). Plus, it is quite expensive, several times that of a P1S in fact. And even if you get it, the design is still in its infancy and lacks simple things like an enclosure and reliable remote monitoring and control. I think Prusa will get there. But I’m starting to wonder if Bambu Lab will get there first and do it better for cheaper. I saw a recent interview where the CEO said they are planning on an XL but are waiting for their next generation technology. A larger print volume plays well with tool changing capability, so my guess would be this is where they are going.
Conclusion
Prusa seems to have gotten caught on their heels. And the advantages of the Bambu Lab printers are particularly noticeable for shoemaking applications. Printing shoe lasts, for instance, is much faster, done remotely, and with filament run-out handled nicely. And there is even sufficient build volume to 3D print entire shoes. The Prusa XL is still very interesting given full tool changer capability, but Prusa has much work to do if they want to keep the lead.
As much as I like Prusa’s open source philosophy, I just find Bambu’s printers significantly better. So for now at least, I’m going to stick with my X1C. All of my upcoming tutorials on 3D printing for shoemakers will revolve around the X1C–at least until something better comes along! So if you want to follow along and are undecided on which printer to get, maybe consider an X1C or P1S along with the AMS.
6 thoughts on “Best 3D Printer for Shoemakers: Bambulab VS Prusa”
I feel that you are giving short shrift to the open source nature of the Prusa MK printers. The real growth of hobby 3d printing owes it’s success to the open source hardware and software community. Companies like Bamboo labs have taken these gifts, monetized them, and have given nothing back to the community. Prusa, on the other hand, has been an absolutely stellar supporter of open source. As such, upgrades for their printers are continuously designed and made freely available. I feel there is value in upgrade over replacement as well but now I’m getting on my soapbox…
I did try to voice my positive sentiments for Prusa’s open source nature, but perhaps I could have gone further. That being said, I think the more prominent story line here is that of a large company getting caught on their haunches, getting spread too thin and focussing on the wrong things, not adapting and listening to what people want. This kind of disruption happens all the time.
What material are you using for the shoes?
TPU
What do you think of the Bambu A1 or the A1 mini? I am a complete beginner at 3d printing and wasn’t sure about starting with the entry level printer or just go straight to a higher model. thanks!
Build volume is a bit small on those…